Digital health & remote patient monitoring for Primsphera with IoTConnect
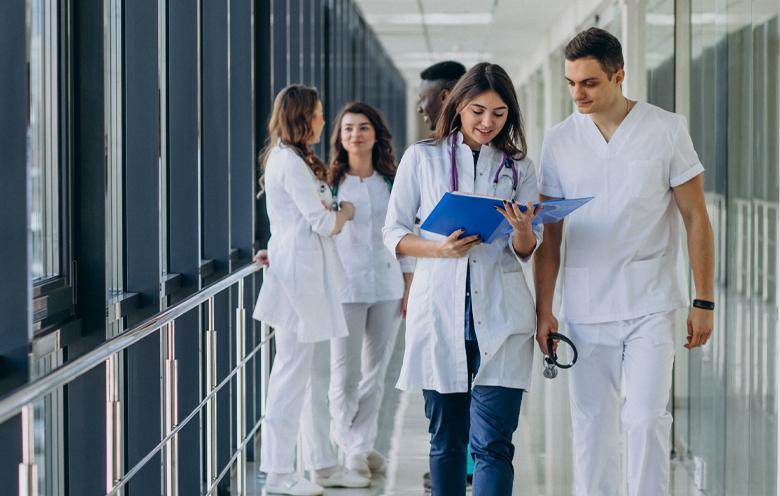
The client is a leading manufacturing company specializing in industrial equipment production. With multiple production facilities across North America, the company operates in high-risk environments where worker safety is a top priority.
Manufacturing
Node.js , Express.js, Angular, React, /IOTCONNECT, Amazon EC2, DynamoDB, Amazon SQS, MySQL
The company faced difficulties managing and analyzing large volumes of safety equipment data, leading to information overload. Real-time response to critical alerts remained an issue, especially for remote or large-scale operations. Moreover, integration into existing enterprise systems required additional technical effort, while connectivity issues had an influence upon GPS tracking and real-time notices. In addition, user adoption was a hurdle because the safety teams required training to fully utilize the features of the safety portal.
After assessing the company’s existing safety infrastructure, our certified AWS consultants provided a strategic roadmap to enhance safety monitoring and optimize workforce protection. Our recommendations focused on improving data management, real-time alerting, system integration, and overall user engagement.
To address these challenges, we implemented advanced data visualization and filtering tools along with our IoT platform, /IOTCONNECT, to simplify safety data analysis. We also introduced an automated alert prioritization to categorize alerts based on severity, ensuring quick response to critical incidents.
Tell us what you are looking for and we will get back to you right away!
Wells Vehicle Electronics is a well-known manufacturer and supplier of electrical parts and components for vehicle manufacturers in North America. The company’s contribution to the automobile industry is remarkable as they have been delivering to this vertical for a long time. They stand for a matchless, customer-focused philosophy, making them one of the most trusted manufacturers in the automobile industry.
For a layman, reading and understanding DTCs (diagnostic trouble codes) is like wheels within wheels. To leverage the vehicle’s self-diagnostic and reporting capability, our client wanted a mobile app that can communicate with the dongle via Bluetooth and interpret DTCs that correspond to the fault.
The main objective of the client was to communicate with the dongle connected to a vehicle and decrease diagnostic time while providing the user with an effective preventive maintenance solution. Some of the common challenges faced by them were:
In the past few years, Bluetooth IoT mobile apps have evolved, enabling modern enterprises to achieve their business goals. The client was also looking for a mobile IoT app that pairs seamlessly with Bluetooth. So, our team of experts built an IoT mobile application called ‘GoTech™ Mobile OBD-II Diagnostics Tool’ that pairs with the OBD-II dongle via a Bluetooth connection. The client wanted a mobile app for car owners or service technicians so that they could purchase the dongle device.
The app fetches and displays information on the faulty codes and various gauges, thus allowing the user to take preventive care. On top of the code’s meaning and the possible causes, the IoT mobile app also provides the user with real-time digital gauges that monitor a vehicle’s engine performance, which includes various parameters, such as:
Ingersoll Rand is a diversified industrial company with manufacturing facilities in over 99 countries. The company manufactures products that are used extensively in the construction, mining, industrial and commercial markets. Some of its popular products are HVAC equipment, pumps, golf cars, compressed air solutions, air compressors, and material handling devices.
Compressors are an essential part of Ingersoll Rand. Their manufacturing process relies on compressors. Hence, it is crucial to run them effectively without failure. The company was unable to constantly monitor them to understand their performance.
It was difficult for the client to gain insights into key parameters of the machines and predict failure beforehand. Running diagnostics and deciding on important aspects like changing damaged parts or forecasting maintenance were a few of the challenges faced by Ingersoll Rand.Softweb Solutions leveraged the benefits of IoT solutions to address these issues. Our data analytics experts thoroughly analyzed each problem statements and suggested Avnet’s IoT platform, /IOTCONNECT®. The platform offers the required infrastructure and smart solutions that help Ingersoll Rand address their business challenges efficiently.
Our data scientists worked to gain insights from their data. The /IOTCONNECT® platform has connectors to gather data from disparate sources. The compressors continuously report the operating status of their internal parameters (oil temperature, oil pressure, stage 1 temperature, motor current, system pressure, etc.) over a secure internet connection. With sensors in place, the IoT platform gets all the data in one place. If any anomaly is detected in the given parameters, maintenance workers are alerted via email notifications for decision-making.
With predictive analytics, Ingersoll Rand can promptly identify the onset of equipment failure and take proactive measures. Equipment issues are detected by threshold values and the operations managers are sent a notification alert with the anomaly details. With information about the repair or maintenance work handy, the company can save on shipping costs, rather than having to bring all the possible components to the customer site.